Graphite is used in molds and mold parts. Graphite has good physical and chemical properties, mainly reflected in: good thermal conductivity and conductivity, high temperature and corrosion resistance, good lubrication and wear resistance, easy processing, and can be used for molds and mold parts with complex structures and high precision requirements.
Graphite material is widely used in glass forming molds. Due to its chemical stability, it is not easy to be soaked by molten glass, and will not change the composition of glass. Graphite material has good heat shock resistance, and its size changes little with temperature. Therefore, in recent years, it has become an indispensable mold material in glass manufacturing. It can be used to make molds for glass tubes, bends, funnels and other kinds of special-shaped glass bottles.
Electrical discharge machining performance: fast speed: light weight, low loss, burr free, easy polishing, low cost
How to choose graphite processing equipment?
(1) High vacuum intensity is required
Graphite processing has strict requirements for machines. Powder not only causes harm to machines, but also causes certain harm to people. Therefore, suggestions for equipment dust absorption strength are:
1) Frequency converter controls the operation of the vacuum cleaner to reduce vibration sources
2) The suction port is close to the processing area for fast suction
3) Regular dust blowing design allows the graphite dust deposited in the corners to be blown up and sucked away, without being trapped inside the machine
4) The tool library door is equipped with a blowing device to prevent graphite dust from entering the tool library and affecting the machining accuracy due to sticking the tool handle
(2) Machine tool sealing is very important
The sealing of the tool magazine, including the design of the Y-axis, must be very strict. If the sealing of the machine tool is not done well, the equipment will enter dust for no more than 3 months, and some electronic components will gradually damage. It is recommended to integrate the design of the Y-axis dust cover and upgrade its protective performance.
(3) Solid rail oil is generally required
Graphite equipment generally uses solid rail oil, but the reason why graphite rail oil still drips oil is that oil stains settle over time, producing waste oil that slowly drips into the graphite or machine. It is recommended to:
1) Once the guide rail oil drips onto the graphite surface, it damages the material;
2) Use a drip oil recovery device, regularly suck oil, and recycle waste oil.
2. Design processing fixtures well
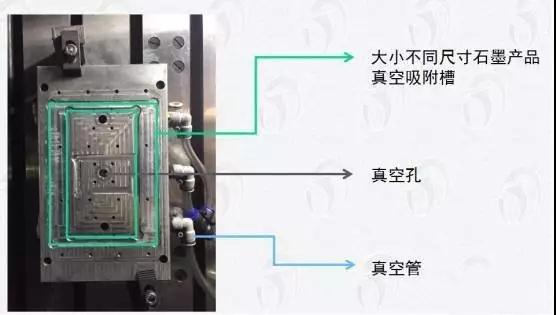
Vacuum fixture
The above image shows a vacuum fixture, which can be used to produce two or more products. At present, many are vacuum adsorption stations, with up to 3-4 large and small ones installed on one machine. Some graphite processing uses tooling, but this is for making mold electrodes; Graphite molds are generally made using vacuum adsorption tables, which have stable processing dimensions and small deformation.
3. Choose the right tool
The difficulty of graphite processing also lies in the cutting tools, which wear very quickly. Ordinary cutting tools in China only take 3-4 hours, and better ones take 5 hours. The imported cutting tools from abroad take about 6-8 hours. When choosing a tool, try to choose a flat bottomed tool with an R blade, and do not choose a flat bottomed tool (for rough and fine trimming). Because the tip of a flat bottomed knife is sharp, cutting graphite can easily collapse. Graphite is relatively hard and brittle, and cutting it too sharply can easily collapse. So when we cut now, we usually choose tools with point R angles (0.5R or 0.2R).
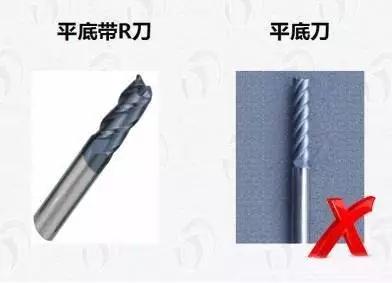
Ball knives are generally used for precision trimming. The maximum loss is in the R knife shown in the figure below. A set of molds takes 2 hours to process, while a finely crafted one takes 3 hours. Currently, efforts are also being made in China to study the material and coating of cutting tools, hoping that the processing time will be longer and the cost will be reduced.
4. Set parameters and select tools at different processing stages
1) Open thick
Rough graphite processing path
The following figure shows a simple graphite processing path, which is the roughening path. Next to it is the enlarged cutting depth of the roughening and the processing amount of each tool.
Parameter settings:
Cutting amount: 2-3mm
Processing speed: 3-4 m/min
Spindle speed: 10000-12000rpm
Tool selection:
Coarse knife: four blade, 10-12mm
(Diameter too small: slow speed, inefficient processing)
(Excessive diameter: large tool swing, affecting machining accuracy)
Coarse rendering
2) Medium thick
Medium coarse graphite processing path
Parameter settings:
Cutting amount: 0.5mm
Processing speed: 3m/min
Spindle speed: 15000rpm
Tool selection:
R-knife: R3 (with curved surface, slightly larger surface, suitable for rough surface cutting)
Medium thick rendering
3) Refinement

Refined graphite processing path
As shown in the above figure, there are many paths for precision machining of climbing surfaces: 0 °, 45 °, 90 °, including circular ones. Currently, the best cutting effect is still 90 °, which is generally better. Generally, the R knife is used for fine trimming, and the effect is also relatively good. However, foreign machine tools use round nose knives, which have high precision requirements for machine tools. The cutting accuracy of products like Makino and Mikron is very high, and using a round nose knife can also make them very bright. Basically, there is no need to polish them when cutting.
Parameter settings:
Cutting amount: 0.03mm
Processing speed: 3m/min
Spindle speed: 22000rpm
Tool selection:
Punch: R Knife: R2 (with small surface, adjustable high speed, low vibration, and improved processing effect)
Die: Round nose knife (flat bottom with R-knife) (6R0.5/4R0.2)
(6&4 represents diameter, 0.5&0.2 represents R angle, and the smaller the R angle, the smaller the processing range and finer the processing. It can handle corner positions in the concave mold.)
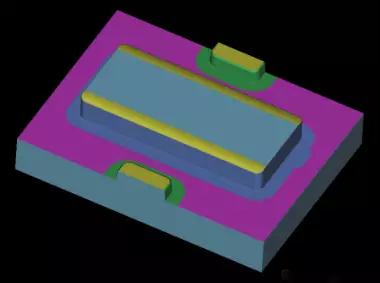
Refined rendering
2、 What problems may be encountered in graphite CNC machining and how to solve them
1. Knife line issues
1) Tool issue: It is recommended to use high-quality tools as much as possible. At present, it is advisable to import more cutting tool materials and coating formulations. The materials and coatings of domestic cutting tools are still under further research.
2) Post processing: A specialized post processing program that works in conjunction with the CNC system.
2. Dark grain problem
Machine tools, cutting tools, etc. can affect accuracy and produce dark lines.
1) System issue: The system settings need to be adjusted, select the "High precision" mode, and cooperate with the system specific post-processing;
2) Knife walking method: It is recommended to move both axes simultaneously instead of moving three axes simultaneously. 45 ° generally uses three axes to move simultaneously, but if the three axes move simultaneously, the effect is not as good and it is easy to produce knife marks.